Whether you are a contractor, architect, engineer or simply a home owner with a concrete foundation you have most likely heard the adage that “all concrete cracks”. While this is true, there are measures that can be taken to greatly reduce the magnitude and frequency of cracks. To do this, one must have an understanding of the factors that lead to cracking. One such factor is stress concentrations in the concrete which are evident at re-entrant corners. Re-entrant corners are defined as any inside corner that forms an angle of 180° or less. In a solid object that is subjected to internal or external loads, re-entrant corners create high stress concentrations. If that solid object is concrete, which is strong in compression but weak in tension, then it will inevitably lead to a crack that will propagate at approximately 135° from the corner. Re-entrant corner cracks are especially prevalent in concrete slabs that are relatively thin in comparison to their plan size. In this article, I will focus on re-entrant corners in slabs-on-grade.
Examples of loads that can induce stress in concrete slabs include:
Reentrant Corners In A Slab
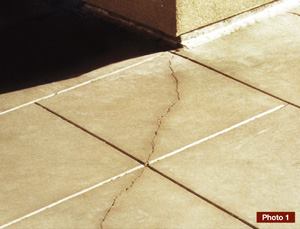
- Shrinkage of the slab during the curing process when the concrete will shrink in volume as the chemical reaction between the cement and water takes place. Depending on the curing methods in place, the top and bottom surface of the slab will cure at different rates which induces stress in the slab.
- Temperature changes. As with all materials, when concrete increases in temperature it will expand and when it decreases in temperature it will shrink. This expansion/shrinkage induces stress in the slab due to restraints such as friction with the bottom of the slab, stiffening ribs, piers etc.
- External loads such as additional material or assemblies placed on top of the slab.
Diagonal cracks that emanate from a corner of a window and other openings are called reentrant cracks and are usually the result of stress built-up at the corner. Recommended Solution: Flexomeric DIY Foundation Crack Repair Kits.
Re-entrant corners should provide a smooth transition between adjacent surfaces, but generally need not be cut exactly to a circular profile. The recommendation in the the 13th Edition AISC Manual, Part 9, is that an approximate minimum radius of 1/2 in. Re-entrant corners are high-stress areas prone to transverse cracking from plastic shrinkage. A re-entrant corner is where any inside corner forms an angle of less than 180 degrees into the body of the slab. As the concrete dries and shrinks, the wedge shape of the re-entrant corner encourages concrete to crack off the point of the angle into.
There are a number of measures that can be utilized to control re-entrant corner cracks including:
- Contraction (Control) Joints: Place contraction joints at the re-entrant corner to create weak planes in the slab that will increase the possibility of cracks forming in the bottom of these contraction joints rather than at ~135° from the corner. Contraction joints can be formed by tooling the joints while the concrete is still plastic or with a saw after the concrete has set. It is important that contraction joints are placed as soon as possible before re-entrant corner cracks begin to form.
- Construction Joints: Placing a construction joint 90° to the interior corner eliminates the re-entrant corner and thus the stress concentration.
- Wet Curing. Wet curing of the slab will slow down the curing process and will create a more uniform cure rate between the top and bottom of the slab. This has the effect of reducing but not eliminating internal stresses. Wet curing can be accomplished by ponding the slab, utilizing foggers to maintain a humid environment on the slab, or by applying a chemical curing compound. In my experience, ponding of the slab is the most effective means of wet curing however it is typically the least practical.
- Water to Cement Ratio: The primary ingredients in concrete are cement, water, fine aggregate and course aggregate. The water chemically reacts with the cement to bind the aggregate in a solid matrix. To fully hydrate cement, a water to cement ratio (w/c ) of 0.26 is required. Additional (free) water is added to the mix to increase the workability of the concrete. As more free water is added to the mix, it increases the shrinkage of the concrete because the free water will eventually evaporate out of the concrete. For our slab-on-grade design, Dudley Engineering typically specifies a maximum w/c ratio of 0.45. Additional workability can be achieved by adding water-reducing admixtures or superplasticizers to the mix.
- Fly Ash: Fly ash is a recycled material that can be utilized in limited quantities to replace cement. Replacing a small portion of the cement with fly ash can have the benefit of reducing the expansion of the concrete during curing.
- Concrete Additives: There are chemical admixtures which can be added to the concrete mix that reduce the shrinkage rate of the concrete. Recently, on a post-tensioned slab-on-grade foundation that was intended to remain exposed, Dudley Engineering specified a shrinkage-reducing admixture in the concrete. This, along with other measures listed above, has produced a slab that is showing no signs of visible cracks.
Reentrant Structure
To have a slab-on-grade foundation that is relatively crack free even at re-entrant corners, a combination of the solutions addressed above should be utilized. In addition to having a more aesthetic slab, it will also exhibit better structural performance throughout the life of the structure.